The energy expenditures of a person during his entire career are determined by the intensity of muscle mass, the level of neuro-emotional stress, and his environment. For a day a man of intellectual labor spends about 12 kJ of energy, for mechanized workers - 13 kJ, but for those who engage in heavy physical labor, it takes up to 25 kJ. At each enterprise there are specialists who are responsible for fulfilling the requirements for hygienic standards of working conditions, which are divided into classes according to the degree of severity, tension, harmfulness and danger of the working environment.
Terminology Issues
Working conditions are a combination of factors of production and the labor process, which have a special impact on the health and performance of each employee.
The production environment is the space in which the worker spends the shift and the labor path.
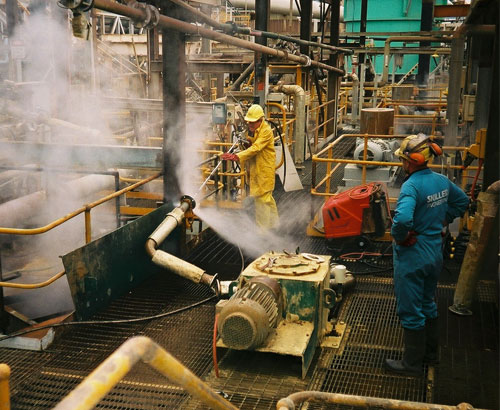
The severity of work is a characteristic of labor, which reflects the predominant load on the motor apparatus and the systems of the human body - cardiac, respiratory and others.
Labor stress is a characteristic that reflects the load on the nervous system, analyzers, emotions, and so on.
Everything that adversely affects human health during work is called harmful working conditions. Hygienic standards for working conditions establish the maximum permissible level of negative factors in the workplace. They are created in order to reduce harmful conditions and protect the health of the employee.
Subject to hygienic standards, the violation of health among employees who are especially sensitive to external factors, for example, in the presence of allergic reactions to dust, pollen and other allergens, is not ruled out.
Hygienic criteria are special indicators that characterize the degree of deviation from the established parameters of the working environment and labor from existing standards.
Hygienic classification of labor and standards of conditions are necessary in order to correctly assess the nature of work in a particular position. Only on the basis of such an assessment can a decision be made that is aimed at preventing and limiting the influence of the adverse environment in the workplace.
Assessment of working conditions
Hygienic standards for working conditions can only be carried out after a special assessment. Based on this, all working conditions are divided into four classes:
- optimal conditions are those where the worker’s health is fully preserved and all the prerequisites are created in order to maintain a high level of working capacity;
- permissible - are characterized by a work environment and a labor process that does not exceed agreed and prescribed hygienic standards at the place of work, and all changes in the functions of the body are easily restored during the rest prescribed by the schedule or before the next shift;
- harmful - are characterized by harmful factors in the workplace, which significantly exceed the hygienic standards of working conditions and are capable of causing an adverse effect on workers' bodies;
- Dangerous - characterized by such working conditions that with a long stay in the workplace, severe forms of acute professional pathologies, poisoning, injuries that pose a serious threat to life can be provoked.
It is also worth saying that harmful factors have several subclasses that allow you to better determine the normal conditions for work:
- harmfulness of the 1st degree - these are conditions affecting the body, but after their influence the functions of the body are restored longer than before the start of the next shift;
- 2nd degree - these are the conditions under which dangerous factors act on an employee, their degree of exposure can provoke persistent changes in the work of internal systems of the body, causing the development of the initial stage of professional pathologies;
- 3rd degree - these are working conditions that can cause persistent disturbances in the body's work, leading to the development of occupational ailments of mild severity with temporary disability;
- 4th degree - these are the conditions under which a worker is exposed to dangerous conditions that cause the development of a chronic form of occupational disease with a loss of ability to work.
When conducting studies of working conditions, all factors harmful and dangerous to the life of the employee must be evaluated at the workplace. These include physical, biological and chemical, as well as labor stress.
Components of working conditions
At any workplace, let it be at an industrial enterprise or in an office building, numerous factors influence any employee. Some of them can cause serious harm to health. All these conditions can be easily divided into several groups:
1. Physical:
- ambient temperature;
- moisture content in the surrounding area;
- wind speed, if work is carried out in the open air;
- magnetic, laser and ultraviolet radiation;
- radiation background;
- noise level;
- ultra- or infrasound;
- high level of dust;
- low light indoors or outdoors;
- vibration.
2. Chemical. Work with harmful substances and mixtures, constant contact with them.
3. Biological. When a person is exposed to temporary or permanent exposure to microorganisms.
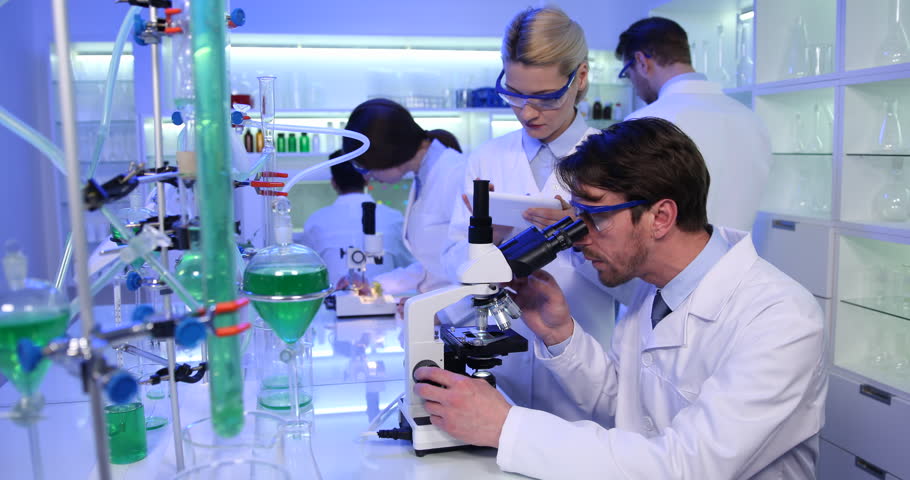
All hygienic standards for working conditions have a certain terminology, which should be easily determined by every worker in any enterprise.
Common abbreviations
When establishing principles and hygienic standards for working conditions, special terms are used. To make it clear, you need to know exactly what their abbreviation and decoding look like:
- GN is hygienic standards.
- MPC - the maximum permissible concentration of harmful substances in the workplace.
- SHOES - tentatively safe exposure levels.
- Remote control - the maximum permissible level of exposure to harmful factors.
- SDA is the maximum permissible dose.
- MPC - maximum permissible concentration, PDU - maximum permissible level. MPC and remote control – hygienic standards of working conditions, the indicators of which are valid for a person throughout the whole working day throughout the entire working experience in a particular production and should not cause diseases and deviations in the health of the employee.
- DNs are permissible loads.
These convenient and understandable abbreviations will allow you to quickly recognize all hygiene standards in any of the industries.
Why conduct a hygienic assessment of working conditions?
The analysis is necessary so that it is possible to identify all possible violations that lead to the fact that the health of the worker suffers. It is possible to identify all conformities or inconsistencies at the workplace only when all necessary measurements are taken using special equipment and tools. This is the only way to correctly assess and establish hygiene standards and classes of working conditions.
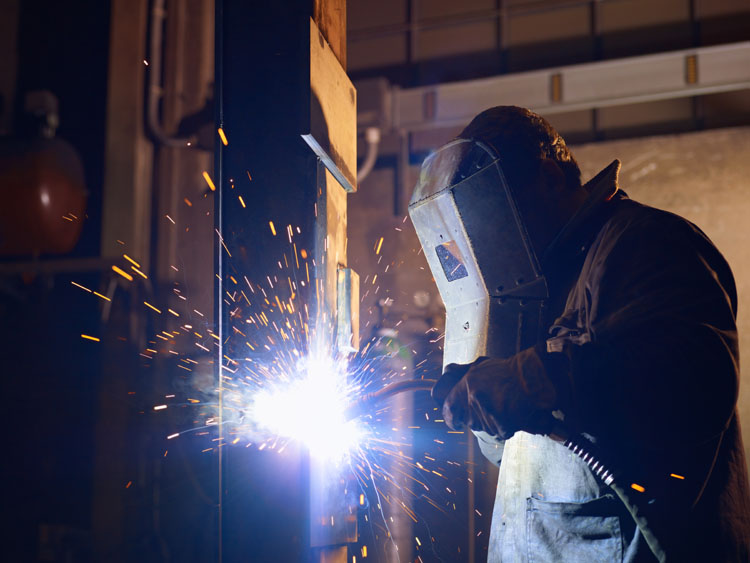
According to statistics, a general description of working conditions can be carried out much more often than once every five years.Many enterprises often see representatives of bodies that check working conditions. It is for this reason that every leader needs to be constantly prepared for the fact that the audit can come at any moment. Constant care of the company’s employees will help not only to avoid constant checks, but also to make production the most convenient and safe. And this will certainly affect labor productivity and the image of the enterprise.
The analysis pursues several main objectives at once:
- assess the compliance of working conditions with hygienic standards with the subsequent issuance of a special sanitary report;
- the implementation of preventive measures to improve working conditions;
- collecting all the necessary information for the database of an individual industry or enterprise;
- classification of jobs in the reserve of working conditions;
- analysis of statistical data on occupational diseases, depending on the specific conditions at a particular workplace;
- assessment of risks to human health at a particular place of work.
After the assessment of sanitary and hygienic standards of working conditions will be carried out, a conclusion is made. General assessment is derived by the maximum class and degree of harmful effects on the human body. Assessment is regulated by document R 2.2.2006-5 “Guidelines for the hygienic assessment of factors of the working environment and the labor process”.
Occupational diseases
Hygienic standards of working conditions provide reliable protection for every worker, because in many enterprises the harmfulness is very high, and it can provoke the development of an occupational disease. Under professional illness means pathology caused by exposure to a harmful environment in the workplace. The acute form of the disease is a variety that occurs after one exposure to a person with harmful occupational factors.
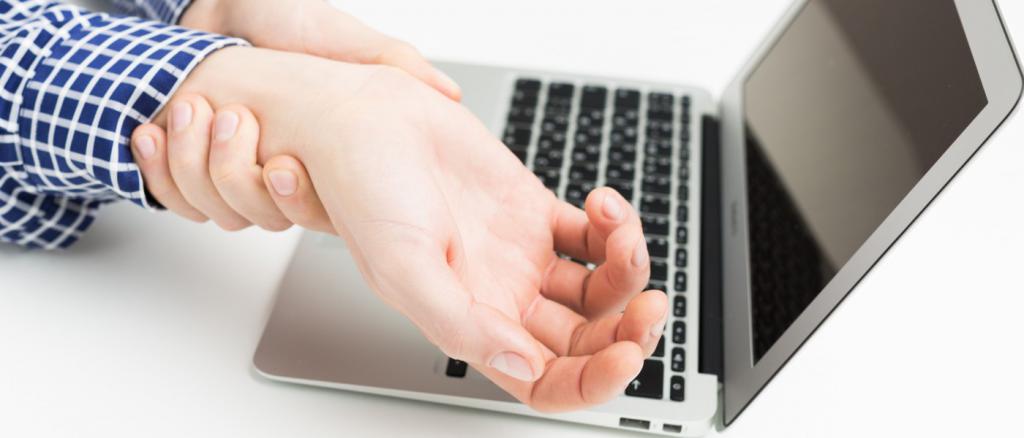
The chronic form of occupational disease occurs after prolonged and repeated exposure to harmful factors of production on the human body.
Occupational poisoning is an acute intoxication that is caused by harmful chemical factors in the work environment.
An acute form of occupational poisoning is a disease provoked after a single exposure to a hazardous chemical component on any employee. Acute forms of poisoning can occur due to accidents, serious violations in technological processes, industrial safety and sanitary conditions, in situations where the concentration of toxic substances significantly exceeds the established norm.
A chronic form of poisoning develops after prolonged constant exposure to small concentrations of a harmful substance.
How to create optimal conditions for an employee? What is meant by hygienic standards of working conditions that are ideal for every working employee of a small or large manufacturing enterprise?
How to ensure comfortable working conditions in the workplace?
The meteorological conditions and microclimate have a special impact on the work of any employee. They directly depend on the thermophysical features of the equipment, season, conditions for maintaining normal temperature and ventilation. The microclimate is determined by the effect on the body of temperature, humidity and air movement, the intensity of thermal radiation.
The main factor in the microclimate is the temperature regime. The change in temperature is affected by the heat that comes from different sources. To ensure comfortable working conditions that do not meet sanitary and hygienic standards, you need to remove and create more comfortable ones. To do this, you need to monitor all factors.What should be the conditions at work in order to avoid the development of occupational diseases and prevent serious violations? Given the specifics of production, indicators may vary slightly.
Air humidity
Humidity is the content of water vapor in the air. It is characterized by several concepts:
- absolute humidity;
- maximum humidity;
- relative humidity.
Relative humidity is taken as 100%. To determine it, they use special tables and graphs that make it easy to find this value.
Air mobility
It is possible to create air mobility in the room by convection flows due to the temperature difference inside and outside, as well as using mechanical ventilation. At present, if desired, the installation of equipment will provide optimal working conditions.
Thermal radiation
Normally, the temperature of the human body is 36.6 degrees. To keep it constantly, there are two types of analyzers on the skin of a person: some react to heat, and others to cold. These receptors protect a person from overheating or hypothermia, help maintain a constant temperature balance. If the company constantly violates the thermal regime, then the employee begins to get sick, undercooling or overheating.
Observing hygiene standards and classes of working conditions even at the most harmful enterprise, you can minimize the aggressive effect on the human body. Each employee working in such a production should regularly undergo examination and visit sanatoriums in order to remove from the body everything that he has been collecting in the body over time.
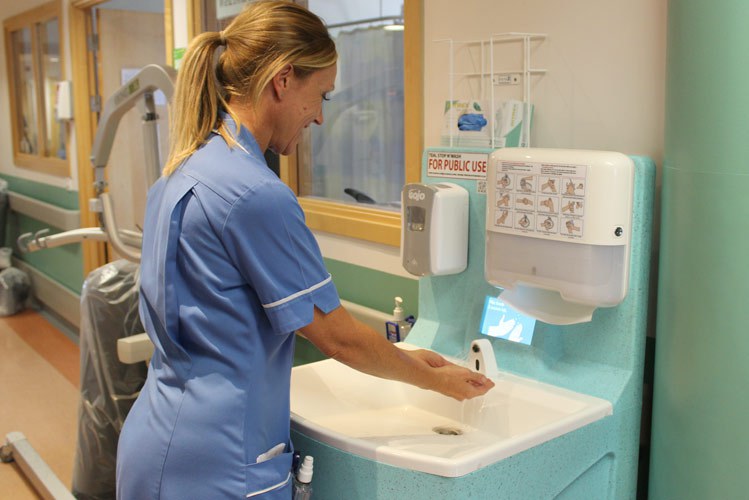
But all responsibility for creating suitable working conditions corresponding to regulatory indicators rests with the employer. Each employee has the right to file a complaint with higher authorities if he considers that his rights are violated.