Im Baugewerbe und in der Industrie sind Schweißarbeiten üblich, sodass Sie langlebige Strukturen und Mechanismen mit unterschiedlichem Komplexitätsgrad zusammenbauen können. In der Phase der Überwachung der resultierenden Naht ist es nicht immer möglich, die Zuverlässigkeit der verbundenen Baugruppe innerhalb der Struktur zu beurteilen. Hierzu werden zerstörungsfreie Prüfverfahren für Schweißverbindungen eingesetzt. Die radiografische Analysemethode ist eine der häufigsten in dieser Nische.
Das Funktionsprinzip der Röntgenkontrolle
Das Verfahren basiert auf der Verwendung von radioaktiver Strahlung, die es ermöglicht, die innere Struktur des Materials zu analysieren, ohne dass ein physikalischer Eingriff mit Verformung erfolgt. Hierfür werden Röntgen- und Gammastrahlen verwendet, die das Produkt durchdringen. Infolgedessen erhält der Bediener eine Karte mit Strukturfehlern, die auf einem magnetografischen Film aufgezeichnet sind. Durch Bestrahlung können Sie ein Bild mit verborgenen Konturen der Struktur erstellen, deren Entschlüsselung bei der Fotobearbeitung von einem speziellen Entwickler durchgeführt wird. In jedem Fall können die Parameter für die Durchstrahlungsprüfung von Schweißverbindungen gemäß GOST 23055-78 variieren - bis zu 6 mm Durchmesser und 1 bis 10 mm Länge in Bezug auf Poren und mangelnde Durchdringung. Wenn die Länge des Gesamtradiogramms weniger als 100 mm beträgt, nimmt die Gesamtfläche der Defekte proportional zur Länge der Karte ab. Die Eindringtiefe von Röntgenstrahlen wird durch die Parameter des Teils bestimmt.
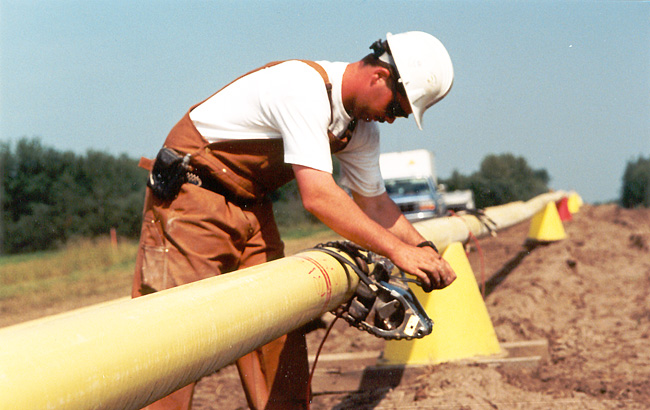
Die Technologie der Röntgenkontrolle wird häufig zusammen mit der Ultraschallmethode zur Analyse der Struktur von Materialien verwendet. Eine solche Kombination tritt üblicherweise in Situationen auf, in denen der Einsatz von Ultraschall technisch nicht möglich ist. Darüber hinaus liefert die Strahlabtastung weitere Informationen zu den geometrischen Daten von Lochfraß- und Korrosionsläsionen. Unterschiede bei der Ultraschall- und Röntgenprüfung von Schweißverbindungen hängen mit der Wirksamkeit der Untersuchung von Fehlern mit unterschiedlichen Formen zusammen. Im ersten Fall konzentriert sich die automatische Ultraschallfehlererkennung eher auf das Arbeiten mit ebenen Fehlern in Form von Fehlern und Rissen. Die Radiographie liefert wiederum eine hohe Genauigkeit bei der Analyse von Volumendefekten.
Ernennung der Röntgenkontrolle
Mit dieser Kontrollmethode wird die Qualität einer Schweißverbindung aus Metallen und Legierungen bewertet, deren Dicke zwischen 1 und 40 cm liegt.Die Fehler werden hauptsächlich in der inneren Struktur der Produkte unter den Bedingungen lokaler Abwesenheit von Fremdeinschlüssen, technologischen Poren und Lot festgestellt. Gemäß GOST sollten Schweißverbindungen zum Zeitpunkt der Inspektion auch frei von Schlacken, Schmelzspritzern, Zunder und anderen Verunreinigungen sein, die während des Schweißprozesses zurückgeblieben sind. Das gebräuchlichste Anwendungsgebiet für die Röntgenüberwachung sind Onshore- und Untergrundrohrleitungen. Die Analyse wird durchgeführt, indem die Strahlen unter Verwendung von Fehlererkennungsgeräten in das Rohr gelenkt werden. In Bezug auf unterirdische Versorgungsunternehmen ist dieses Abtastverfahren dahingehend vorteilhaft, dass es keine Öffnung von Kanälen mit Erdarbeiten erfordert.
Es ist hervorzuheben, in welchen Situationen die Verwendung der Röntgenkontrolle aufgrund technischer und struktureller Einschränkungen unwirksam oder überhaupt nicht zulässig ist:
- Verschiedene Arten von Einschlüssen und Unstetigkeiten, deren Größe in Durchlichtrichtung kleiner ist als die doppelte Empfindlichkeit der Kontrolle.
- Einschlüsse und Unstetigkeiten, die nahe an scharfen Ecken, Unterschieden oder Fremdteilen liegen, sind technologisch vorgesehen. In den Röntgenbildern wird das Zusammentreffen von Defekten und Strukturelementen keine genaue Bestimmung der Eigenschaften der inneren Struktur ermöglichen.
- Risse und fehlende Verschmelzung, bei denen das Flugzeug nicht mit den Übertragungslinien übereinstimmt. In diesem Fall kann eine Kombination von Röntgenabtastung mit zerstörenden Testelementen verwendet werden.
Arten der verwendeten radiometrischen Geräte
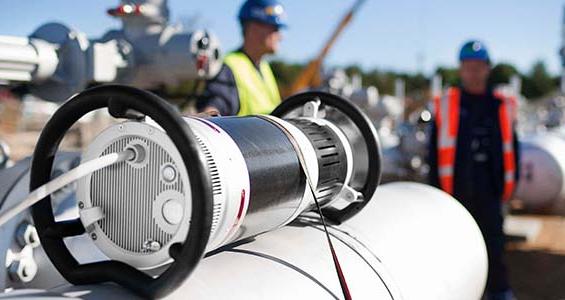
Bisher werden folgende Arten von Geräten für die Röntgenüberwachung aktiv eingesetzt:
- Geräte mit einer konstanten Frequenz von Gammastrahlung mit einer festen Intensität. Frequenzabweichungen verursachen Produktfehler, die sich in den Radiogrammen widerspiegeln. Die neuesten Modelle solcher Geräte sind mit Programmen ausgestattet, die Schwingungsspektren genau bestimmen.
- Röntgengeräte mit Unterstützung für zeitlich zufällige hochfrequente Schwankungen. Der Schwankungsgrad kann in Abhängigkeit von der Strahlungsintensität 0,5-1% überschreiten.
- Geräte zur Durchstrahlungsprüfung von Schweißverbindungen, deren Stabilität der Gammastrahlung mehr als 0,5% beträgt. In diesem Fall liegt die Schwingungsamplitude innerhalb von 0,1 Hz. Ein solches Gerät ist optimal für das dünne Abtasten von Defekten mit kleinem Volumen, es ist jedoch nicht zweckmäßig, es für die Analyse tiefer Fehler in großen Bereichen zu verwenden.
In Bezug auf die Steuerung unterstützen fast alle Geräte automatisierte Tools mit der Möglichkeit, die empfangenen Daten bei der Erstellung von Radiogrammen programmgesteuert anzupassen.
Vorbereitung für die Röntgeninspektion
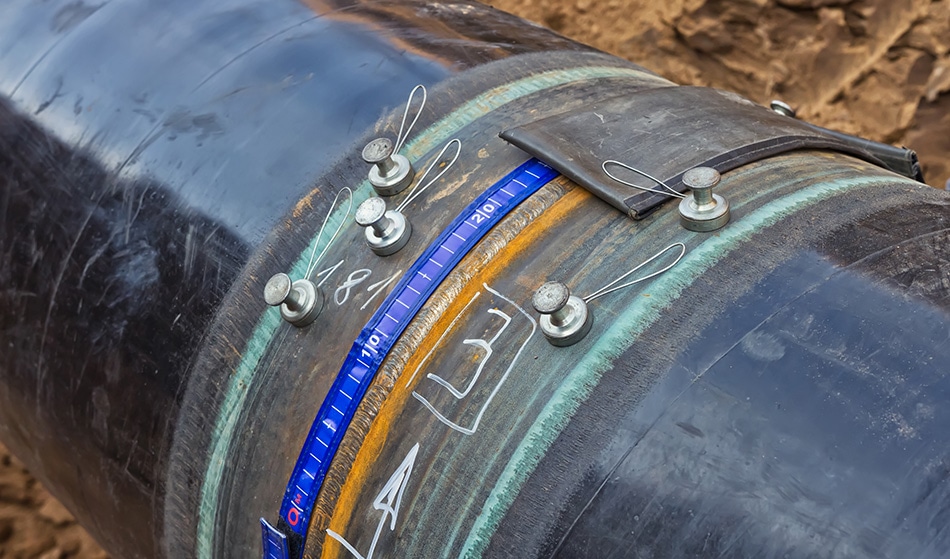
Vor dem Scannen wird besonderes Augenmerk auf den Zustand des Produkts und direkt auf die Schweißnaht gelegt. Der Bediener prüft das Teil auf äußere Mängel, entfernt Verunreinigungen und markiert gegebenenfalls die Bereiche. Große Bereiche zum Scannen sind durch Zonen gekennzeichnet und unbedingt nummeriert. Ferner werden in kontrollierten Bereichen Standards mit Empfindlichkeitsmarkierung festgelegt. Beispielsweise sollten Rillennormale in Querrichtung 5 mm von der Nahtlinie entfernt platziert werden. Um das zuverlässigste Ergebnis bei der Qualitätskontrolle von Schweißverbindungen zu erzielen, können Karten aus früheren Studien verwendet werden. Sie werden im Voraus vorbereitet und vor dem Scannen in das Radiogrammsystem des Geräts eingegeben. Bilder von neuen Bildern werden mit Schwerpunkt auf früheren Daten erstellt. Die Software weist das grafische Scannen auch an, um vorhandene Fehler zu berücksichtigen, und liefert eine separate Informationsschicht über den Grad des Fortschritts derselben Diskontinuitäten, Risse und mangelnder Verschmelzung.
Bestimmung der Kontrollparameter
Nach der Herstellung des Produkts werden die optimalen Eigenschaften seiner Untersuchung durch die Abtastvorrichtung ausgewählt. Einer der wichtigen Parameter ist der Abstand von der Quelle der Gammastrahlung zur Oberfläche des Zielbereichs sowie die Anzahl und Größe der kontrollierten Bereiche. Nach GOST werden Schweißnähte mit Röntgengeräten unter folgenden Einschränkungen gescannt:
- Die Zunahme der Größe von strukturellen Defekten, die sich auf der Seite der Strahlungsquellenvorrichtung befinden, sollte nicht höher als der Koeffizient von 1,25 sein.
- Der Winkel zwischen der Normalen zum fotografischen Film und der Richtung der Gammastrahlung sollte 45 ° nicht überschreiten, wenn er innerhalb eines kontrollierten Bereichs untersucht wird.
- Unschärfebildfehler beim Auflegen des Films für Bilder in der Nähe der Schweißnaht sollten nicht höher als die Hälfte der festgelegten Empfindlichkeit sein.
- Die Länge der Bilder bei der Durchstrahlungsprüfung von Schweißnähten sollte Bilder benachbarter Abschnitte gemäß der Kennzeichnung erfassen.Wenn die Länge des kontrollierten Bereichs innerhalb von 100 mm liegt, beträgt die Überlappung mindestens 0,2 der Gesamtlänge des Diagramms, und wenn der Abstand mehr als 100 mm beträgt, sollte der Griff mindestens 20 mm betragen.
- Für den Fall, dass die Abmessungsparameter der Defekte nicht bestimmt werden, können die Anforderungen zur Aufrechterhaltung des Verhältnisses zwischen dem äußeren und dem inneren Durchmesser der Verbindung ignoriert werden.
Röntgenuntersuchungsschemata von Schweißverbindungen
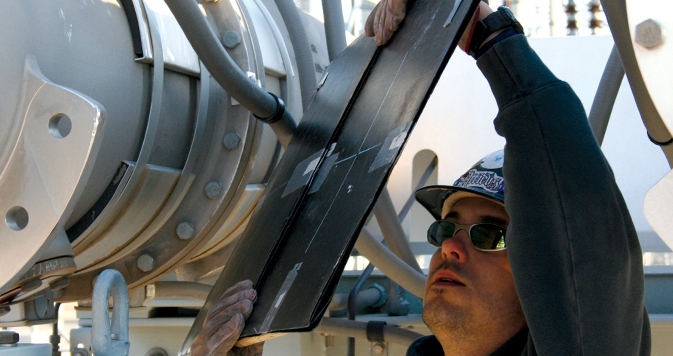
Die Wirksamkeit der Kontrolle wird durch das Transmissionsmuster der Produktstruktur bestimmt. Daher wird beim Abtasten von Ringnähten von kugelförmigen und zylindrischen Teilen üblicherweise eine Durchleuchtung durch die Wand des Elements verwendet. Darüber hinaus befindet sich die Quelle der Röntgenstrahlung im Inneren des Produkts, sodass Sie die Karte der Fehler genauer bestimmen können. Wenn der Durchmesser des zylindrischen Hohlteils 2 m nicht überschreitet, wird eine Röntgenprüfung der Schweißverbindungen mit Panoramaschemata durchgeführt. Es ist jedoch zu beachten, dass in diesem Fall keine selektive Analyse der internen Struktur möglich ist.
Beim Abtasten von Stoßfugen stimmt die Durchlichtrichtung mit der Ebene des untersuchten Bereichs überein. Ein solches Schema wird beim Arbeiten mit eckigen Knoten des Eindringens von Formstücken und Rohren verwendet. Der Winkel zwischen der Strahlung und der Übergangsebene sollte 45 ° nicht überschreiten. Neben Standardkonfigurationen werden auch andere Richtungen der Fehlerübertragung verwendet.
Bei der Auswahl eines Schemas für das Röntgenverfahren zur Kontrolle von Schweißverbindungen werden der Abstand von der Zielanalyseoberfläche zum Film des Geräts (nicht mehr als 150 mm) und die Belichtung mit einem 45-Grad-Winkel in Strahlungsrichtung berücksichtigt. Durch eine richtig ausgewählte Taktik der Bildgebung wird eine informative und genaue Karte mit Fehlern im problematischen Produkt erstellt.
Dekodierung von Röntgenbildern
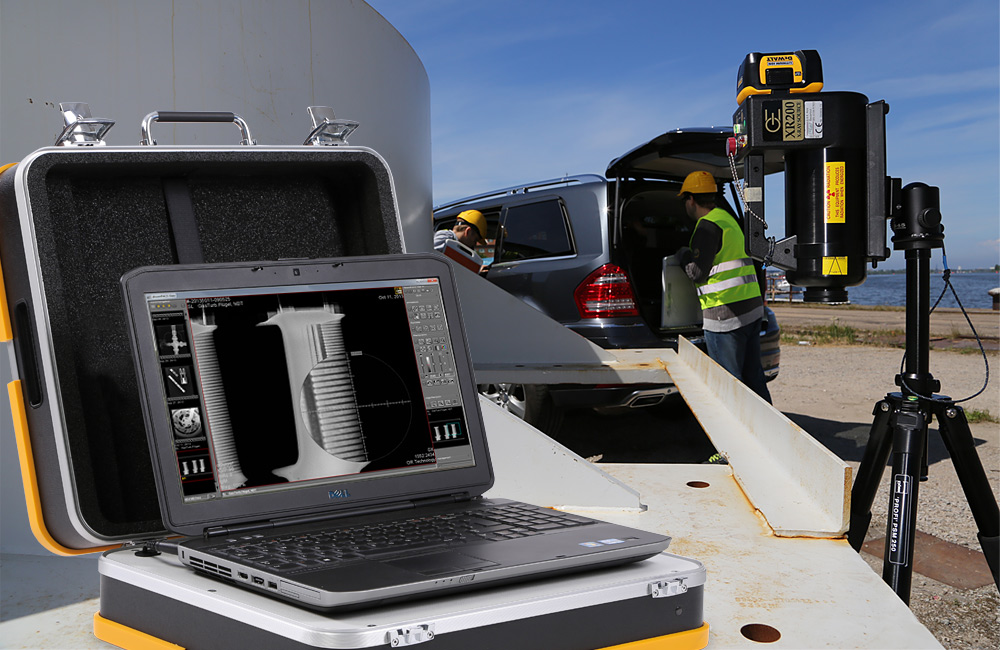
Das Betrachten von Bildern erfolgt nach dem Trocknen in einem dunklen Raum mit Illuminator-Negatoskopen, mit denen Sie die Helligkeit und die Parameter des beleuchteten Feldes einstellen können. Hierbei werden besondere Anforderungen an die Materialqualität gestellt:
- Keine Streifen, Flecken, Beschädigungen und Verunreinigungen auf der Oberfläche der Emulsionsschicht. Alles, was die Entschlüsselung erschwert, sollte nicht auf dem Bild sein.
- Zusätzlich zu den Konturen von Fehlern sollten Markierungen, Markierungen und Grenzstrukturlinien, falls vorhanden, reflektiert werden.
- Die optische Dichte der Grafikkarte, die bei der Qualitätskontrolle von Schweißnähten im Bereich der Naht entsteht, sollte mindestens 1,5 betragen.
Die Bildverarbeitung kann auch auf Scancomputern mit der Erzeugung von Fehlermodellen durchgeführt werden. In diesem Fall erhöht sich die Genauigkeit der Bestimmung des Ortes und der Größe der Beschädigung in der Struktur.
Trennung von Arten von Schweißverbindungen nach den Ergebnissen der Kontrolle
Gemäß den Ergebnissen der Daten in den Bildern wird jeder Naht eine bestimmte Klasse zugeordnet, die von der Größe des Fehlers abhängt. Entsprechend den behördlichen Anforderungen basiert die Klassifizierung auf Porengrößen sowie Oxid-, Schlacke- und Wolframeinschlüssen. Beispielsweise soll bei einer Produktdicke von bis zu 3 mm je nach Gesamtlänge des Defekts eine Unterteilung in Schweißnähte von 3 bis 10 mm erfolgen. Wenn es sich um Teile mit einer Dicke von 200 bis 400 mm handelt, variiert der Klassifizierungsbereich für denselben Parameter zwischen 10 und 90 mm. Beträgt die Länge des Radiogramms weniger als 100 mm, werden die berechneten Daten zur Größe der einzelnen Einschlüsse und Poren proportional zur Größe des Bildes reduziert. Darüber hinaus sollte die Länge der Cluster gemäß den Anforderungen 1,5 relativ zu den maximal zulässigen Längen für einzelne Poren und Diskontinuitäten nicht überschreiten.
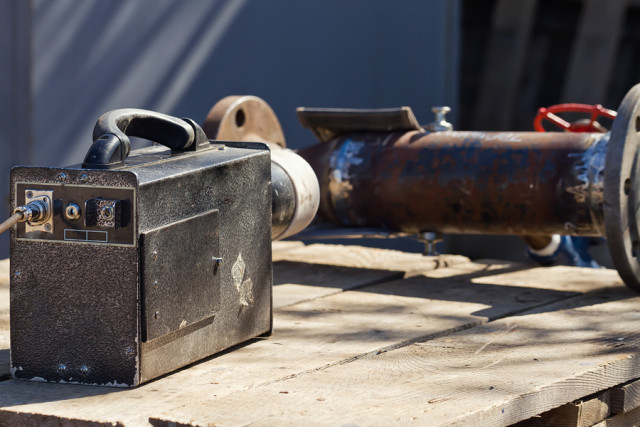
Nach der Verarbeitung der Röntgenkontrollmaterialien wird ein spezieller Akt erstellt, der die Produktdaten und die darin enthaltenen Mängel angibt.Zunächst werden die Eigenschaften des Teils oder der Struktur unter Angabe der zuvor festgelegten Normen und gekennzeichneten Bereiche beschrieben. Die Durchstrahlungsprüfung von Schweißverbindungen kann Daten zu Kapazität, Produktdicke und anderen technischen und strukturellen Indikatoren enthalten. In Bezug auf Informationen zu Defekten wird die gesamte Liste der Informationen, die als Ergebnis der Decodierung von Röntgenbildern erhalten wurden, in speziellen Spalten eingegeben.
Vorsichtsmaßnahmen für die radiographische Sicherheit
Die größte Gefahr bei der Durchführung einer Röntgenuntersuchung besteht in den durch Gammastrahlung freigesetzten Gasen. Zunächst ist hervorzuheben, wie wichtig die Kontrollbedingungen sind, die die Anforderungen für die Verwendung radioaktiver Quellen erfüllen müssen. Die verwendeten elektrischen Betriebsmittel müssen in gutem Zustand sein und möglichst unmittelbar vor der Analyse der Schweißverbindung geprüft werden. Die industrielle Radiographie unterliegt erhöhten Anforderungen an die Gewährleistung der elektrischen Sicherheit. Dies gilt für Situationen, in denen leistungsstarke stationäre Geräte verwendet werden, die an dreiphasige Stromnetze angeschlossen sind. In die Infrastruktur werden zwangsläufig Mittel zur Spannungsstabilisierung und Kurzschlussschutzeinheiten eingeführt.
Vor- und Nachteile der Röntgenüberwachung
Die Radiographie bietet eine Vielzahl von Möglichkeiten zur Fehlererkennung von Schweißnähten, so dass mit hoher Genauigkeit und Bequemlichkeit die kleinsten Fehler in der Struktur von Metallstrukturen analysiert werden können. Bilder auf Röntgenbildern sind so nah wie möglich an der Optik, sodass sie nicht nur von Fehlerdetektoren, sondern auch von den Schweißern selbst analysiert werden können. Zur Interpretation der Ergebnisse werden spezielle Atlanten mit Klassifizierungen ausgegeben, nach denen Sie leicht eine schnelle Beurteilung der Mängel vornehmen können. Zu den Nachteilen der Röntgenprüfung von Schweißverbindungen gehören die Empfindlichkeit für die Erkennung ebener Unstetigkeiten und die geringe Zuverlässigkeit beim Scannen von Fehlern und Rissen. Hinzu kommen Strahlung und hohe finanzielle Kosten, die mit dem Einsatz hochentwickelter Geräte in nahezu allen Kontrollphasen verbunden sind.
Fazit
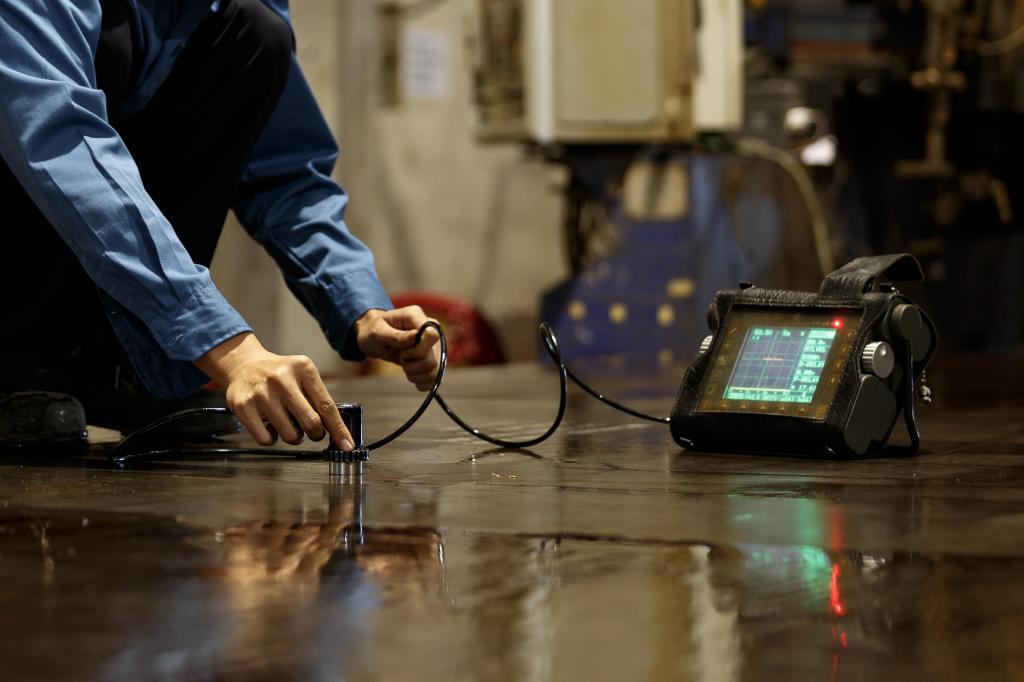
Gegenwärtig ist die Radiographie zwar hinsichtlich der betrieblichen Vorteile nicht die attraktivste, aber eine sehr bequeme und effektive Methode zur zerstörungsfreien Prüfung von Schweißnähten. Es genügt zu sagen, dass im Energiesektor für die Röntgenkontrolle von Schweißverbindungen von Rohrleitungen etwa 30% aller Fälle der Analyse von Fernleitungen zur Feststellung von Defekten erforderlich sind. Die engste Konkurrenz zu dieser Methode ist die Ultraschallprüfung. Faktoren wie die Notwendigkeit der technologischen Aufrüstung von Unternehmen durch den Ersatz teurer Geräte und die eingeschränkten Scanfähigkeiten von Ultraschall behindern jedoch immer noch die vollständige Verdrängung der Radiographie. In einigen Bereichen ist eine Röntgenüberwachung daher nach wie vor unerlässlich.